1. |
Drain the differential gear
oil. |
2. |
Remove the rear drive
shaft. |
3. |
Remove the propeller
shaft. |
4. |
Support the differential assembly (A) with
the jack (B).
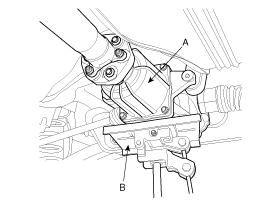
|
5. |
Disconnect the coupling control connector
(A).
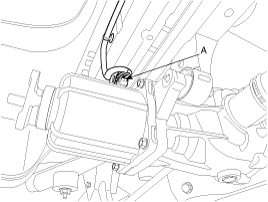
|
6. |
After loosen the differential mounting bolts
(A), and remove the differential (B).
Tightening
torque Nm (kgf-m, lb-ft) :
68.6~88.3 (7~9,
50.6~65.1)
|
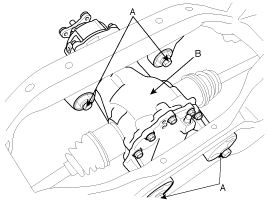
|
7. |
After loosen the cover bolts (A), and remove
the differential cover (B).
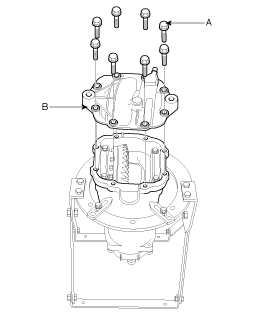
|
1. |
After apply liquid gasket, install the
differential cover (B), and install the mounting bolts
(A).
Tightening
torque Nm (kgf-m, lb-ft) :
39.2~49.0 (4~5,
28.9~36.2)
|
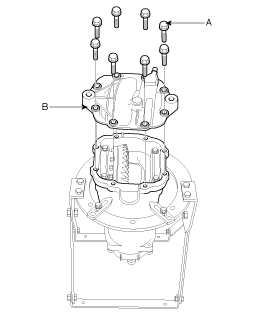
|
2. |
After install the differential (B), and
install the mounting bolts (A).
Tightening
torque Nm (kgf-m, lb-ft) :
68.6~88.3 (7~9,
50.6~65.1)
|
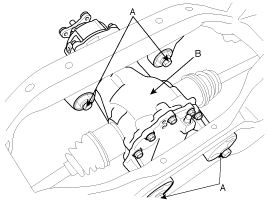
|
3. |
Using the transaxle jack (B), install the
differential assembly (A).
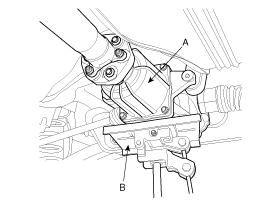
|
4. |
Connect the coupling control connector
(A).
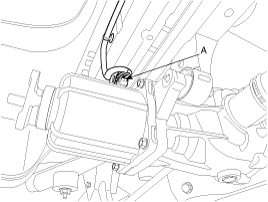
|
5. |
Install the propeller
shaft. |
6. |
Install the rear drive
shaft. |
7. |
Fill the gear oil.
Specified
lubricant:
Hypoid gear oil (API GL-5, SAE
75W/90)
Oil quantity : Fill the reservoir to
the filler plug hold (About 0.9 L)
|
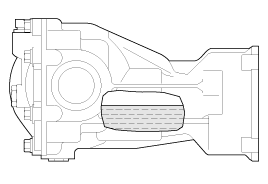
|
8. |
Check the alignment. (Refer to SSgroup
'Tires/Wheels - alingment') |
Inspection
Install the
differential carrier assembly(A) with the special tools(09517-43401 &
09517-43500).Then carry out the following inspection.
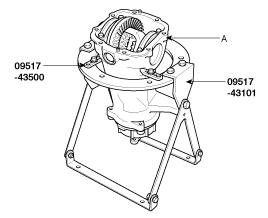
1. |
Check the final drive gear backlash by the
following procedure.
(1) |
Place the drive pinion and move the
drive gear to check backlash is within the standard
range.
Measure at 4 points on the gear
periphery. |
Standard value :
0.10 ~ 0.15mm (0.0039 ~
0.0059in.)
|
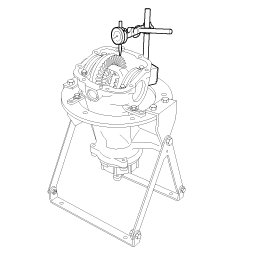
| |
2. |
Check the drive gear back-face lash by the
following procedure.
(1) |
Place a dial gauge on the back-face of
the drive gear and measure the runout.
Limit : 0.05 mm (0.002 in)
|
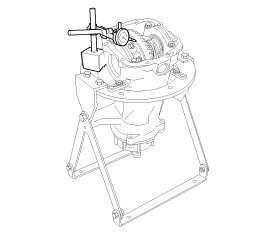
|
(2) |
If the runout is beyond the limit,
check that there are no foreign substances between the drive
gear and differential case and, that the bolts fixing the
drive gear are not
loose. | |
3. |
Check the differential gear backlash by the
following procedure.
(1) |
Fix the side gear with a wedge so it
cannot move and measure the differential gear backlash with a
dial indicator on the pinion gear.
Standard value :
0 ~ 0.05 mm (0 ~ 0.002
in)
|
Take the measurements at two
places on the pinion
gear. |
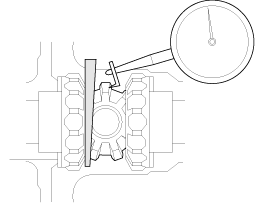
|
(2) |
If the backlash exceeds the limit,
adjust using side bearing spacers.
If adjustment is impossible,
replace the side gear and pinion gear as a
set. | | |
4. |
Check the tooth contact of the final drive
gear by the following procedure.
(1) |
Apply the same amount of machine blue
slightly to both surfaces of the drive gear
teeth.
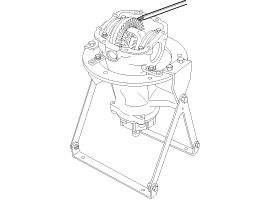
|
(2) |
Insert a brass rod between the
differential carrier and the differential case, and then
rotate the companion flange by hand (once in the normal
direction, and then once in the reverse direction) while
applying a load to the drive gear so that some torque
(approximately 25~30Nm) is applied to the drive
pinion.

If the drive gear is rotated too
much, the tooth contact pattern will become unclear and
difficult to
check. | |
(3) |
Check the tooth contact
pattern.
Tooth
contact
|
Contact
state
|
Solution
|
Standard contact
|
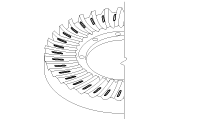
|
|
|
1. Heal contact
|
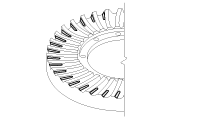
|
Increase the thickness of
the pinion height adjusting shim, and position the drive
pinion closer to the center of the drive
gear.
Also, for
backlash adjustment, reposition the drive gear further
from the drive pinion.
|
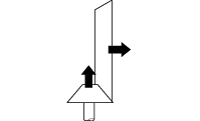
|
2. Face contact
|
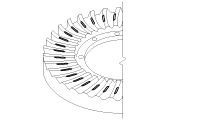
|
3. Toe contact
|
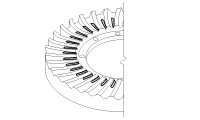
|
Decrease the thickness of
the pinion height adjusting shim, and position the drive
pinion further from the center of the drive
gear.
Also, for
backlash adjustment, reposition the drive gear closer to
the drive pinion.
|
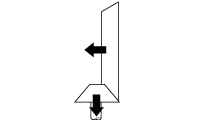
|
4. Flank contact
|
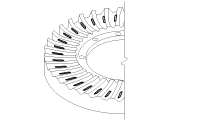
|
• |
Tooth contact pattern is a
method for judging the result of the adjustmentof
drive pinion height and final drive gear backlash.
The adjustment of drivepinion height and final
drive gear backlash should be repeated until the
toothcontact patterns are similar to the standard
tooth contact
pattern. |
• |
When you cannot obtain a
correct pattern, the drive gear and drive
pinionhave exceeded their limits. Both gears
should be replaced as a
set. | | | |
5. |
Check the oil leaks and the lip part for
chew or wear. |
6. |
Check the bearings for wear or
discoloration. |
7. |
Check the gear carrier for
cracks. |
8. |
Check the drive pinion and drive gear for
wear or cracks. |
9. |
Check the side gears, pinion gears and
pinion shaft for wear or damage. |
10. |
Check the side gear spline for wear or
damage. |