1. |
Loosen the wheel nuts slightly.
Raise the vehicle, and make sure it is
securely supported. |
2. |
Remove the front wheel and tire (A) from the
front hub (B).
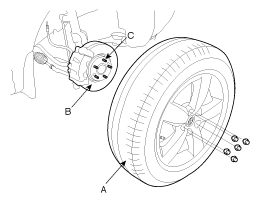
Be careful not to damage to the hub
bolts (C) when removing the front wheel and tire
(A). | |
3. |
Remove the split pin (A), then remove castle
nut (B) and washer (C) from the front hub under applying the
brake.
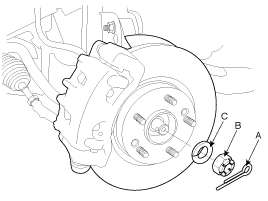
|
4. |
Remove the brake caliper mounting bolts (A),
and then place the brake caliper assembly (B) with
wire.
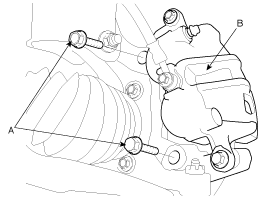
|
5. |
Remove the tie rod end ball joint from the
knuckle.
(1) |
Remove the split pin
(A). |
(2) |
Remove the castle nut
(B). |
(3) |
Disconnect the ball joint (C) from
knuckle (D) using the special tool (09568-4A000).
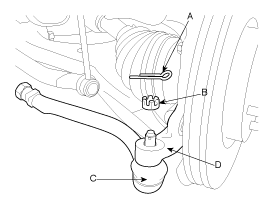

Apply a few drops of oil to the
special tool. (Boot contact
part) | | |
6. |
Remove the split pin and the lower arm
mounting bolt (B) from the knuckle (A).
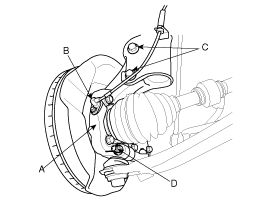
|
7. |
Using a plastic hammer (A), disconnect
driveshaft (C) from the axle hub (B).
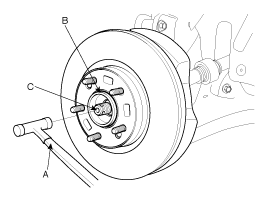
|
8. |
Push the axle hub (A) outward and separate
the driveshaft (B) from the axle hub (A).
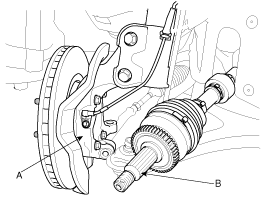
|
9. |
Remove the dust cover (A). (RH
side)
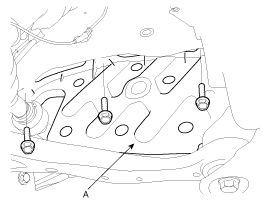
|
10. |
Remove the mounting bolts of inner shaft
bearing bracket assembly (A).
[Gasoline
3.8]
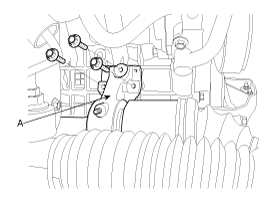
|
11. |
Separate the driveshaft (A) from the
transaxle case (B).
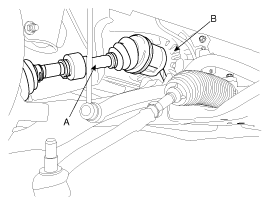
• |
Do not use a pry bar to remove
the driveshaft, as this may cause damage to the dust
cover (A) and dust seal.
Remove the driveshaft after
striking a pipe added on the joint case (B) with a
hammer to prevent damage.
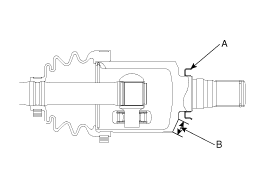
|
• |
Do not pull the driveshaft by
excessive force it may cause components inside the joint
kit to dislodge resulting in a torn boot or a damaged
bearing. |
• |
Plug the hole of the transaxle
case with the oil seal cap to prevent
contamination. |
• |
Support the driveshaft
properly. |
• |
Replace the retainer ring
whenever the driveshaft is removed from the transaxle
case. | | |
1. |
Apply gear oil on the oil seal contacting
surface (B) of transaxle case and the driveshaft splines
(A).
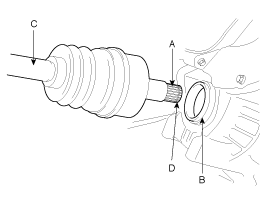
|
2. |
Before installing the driveshaft (C), set
the opening side of the circlip (D) facing
downward. |
3. |
After installation, check that the
driveshaft (C) cannot be removed by
hand. |
4. |
Install the inner shaft bearing bracket
assembly (A) and then tighten the mounting bolts.
Tightening
torque Nm (kgf-m, lb-ft) :
49.0~68.6 (5~7,
36.2~50.6)
|
[Gasoline
3.8]
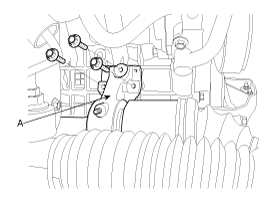
|
5. |
Install the dust cover (A). (RH
side)
Tightening
torque Nm (kgf-m, lb-ft) :
7.8~11.8 (0.8~1.2,
5.8~8.7)
|
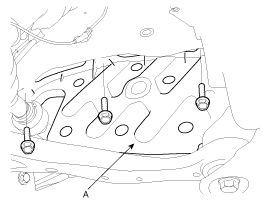
|
6. |
Install the driveshaft to the axle
hub. |
7. |
Install the lower arm mounting bolt (B) and
the split pin to the knuckle (A).
Tightening
torque Nm (kgf-m, lb-ft) :
98.1~117.7 (10~12,
72.3~86.8)
|
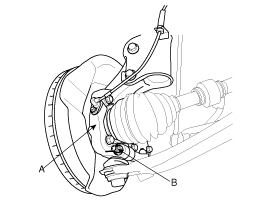
|
8. |
Install the tie rod end ball joint (C) to
the knuckle (D). |
9. |
Install the castle nut (B) and the split pin
(A).
Tightening
torque Nm (kgf-m, lb-ft) :
23.5~33.3 (2.4~3.4,
17.4~24.6)
|
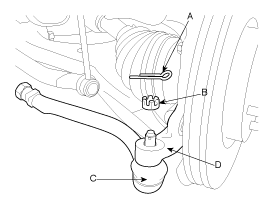
|
10. |
Install the brake caliper (B) and then
tighten the mounting bolts (A).
Tightening
torque Nm (kgf-m, lb-ft) :
73.5~83.4 (7.5~8.5,
54.2~61.5)
|
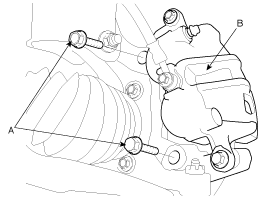
|
11. |
Install the washer (C), castle nut (B) and
split pin (A) to the front hub assembly.
Tightening
torque Nm (kgf-m, lb-ft) :
196.1~274.6 (20~28,
144.7~202.5)
|
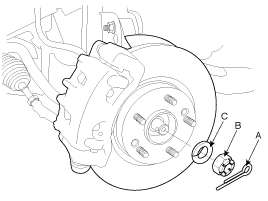
The washer (C) should be assembled
with convex surface outward when installing the castle nut (B)
and split pin (A). |
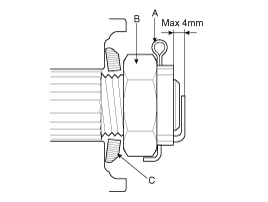
|
12. |
Install the wheel and tire (A) to the front
hub (B).
Tightening
torque Nm (kgf-m, lb-ft) :
88.3~107.9 (9~11,
65.1~79.6)
|
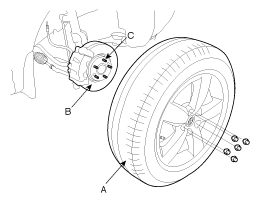
Be careful not to damage the hub bolts
(C) when installing the front wheel and tire
(A). | |
13. |
Check the alignment. (Refer to SSgroup
'Tires/Wheels - alingment') |
1. |
Check the driveshaft boots for damage and
deterioration. |
2. |
Check the ball joint for wear and
damage. |
3. |
Check the splines for wear and
damage. |
4. |
Check the dynamic damper for cracks, wear
and position.
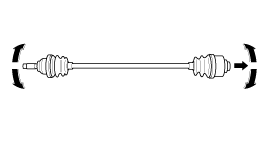
|
5. |
Check the driveshaft for cracks and
wears. |
•
|
Do not disassemble the BJ
assembly. |
•
|
Special grease must be applied to the
driveshaft joint. Do not substitute with another type of
grease. |
•
|
The boot band should be replaced with
a new
one. | |
1. |
Remove the circlip (B) from driveshaft
splines (A) of the transaxle side PTJ case.
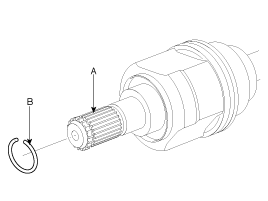
|
2. |
Remove the both boot clamps from the
transaxle side PTJ case.
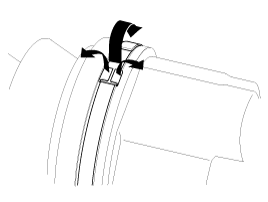
|
3. |
Pull out the boot from the transaxle side
joint(PTJ). |
4. |
Remove the clip (C) from the PTJ case
(B). |
5. |
While dividing joint(PTJ) boot (A) of the
transaxle side, wipe the grease in PTJ case (B) and collect them
respectively.
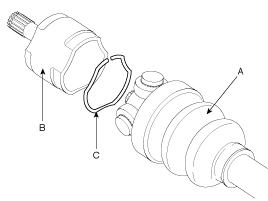
• |
Be careful not to damage the
boot. |
• |
According to below the
illustrated, put marks (D) on roller of trunion assembly
(A), PTJ case (B) and spline part (C), for providing
assembly. |
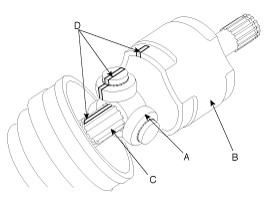
| |
6. |
Using a snap ring plier or flat-tipped (-)
screwdriver, remove the circlip (A).
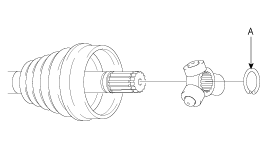
|
7. |
Remove the trunion assembly (B) from the
driveshaft (A) using the special tool (09495-33000).
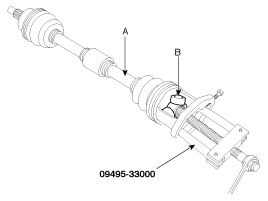
|
8. |
Clean the trunion
assembly. |
9. |
Remove the boot (A) of the transaxle side
joint(PTJ).
For reusing the boot (A), wrap tape
(B) around the driveshaft splines (C) to protect the boot
(A). |
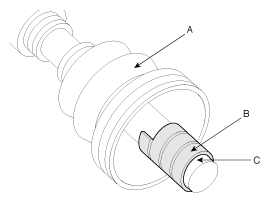
|
10. |
Using a plier or flat-tipped (-)
screwdriver, remove the both side of clamp (B) of the dynamic damper
(A).
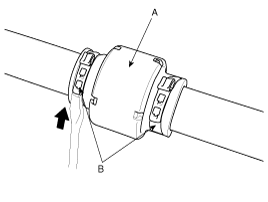
|
11. |
Fix the driveshaft (A) with a vice (B) as
illustrated.
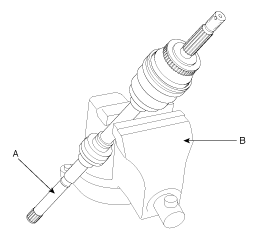
|
12. |
Apply soap powder on the shaft to prevent
being damaged between the shaft spline and the dynamic damper when
the dynamic damper is removed. |
13. |
Saperate the dynamic damper (A) from the
shaft (B) carefully.
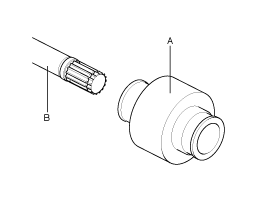
|
14. |
Using a plier or flat-tipped (-)
screwdriver, remove the clamp on the side of wheel.
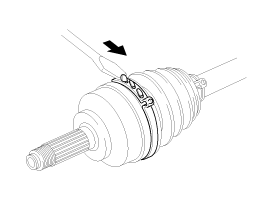
|
15. |
Pull out the joint(BJ) on the side of wheel
into the transaxle direction.
Be carefull not to damage the
boot. |
1. |
Check the driveshaft boots for damage and
deterioration. |
2. |
Check the ball joint for wear and
damage. |
3. |
Check the splines for wear and
damage. |
4. |
Check the dynamic damper for cracks, wear
and position.
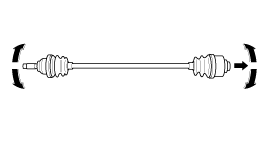
|
5. |
Check the driveshaft for cracks and
wears. |
1. |
Wrap tape around the driveshaft splines
(PTJ. side) to prevent damage to the
boots. |
2. |
Apply grease to the driveshaft and install
the BJ boots. |
3. |
Install the bands to both BJ
boots.
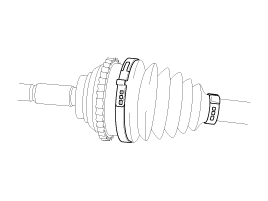
|
4. |
Using the SST(09495-3K000), secure the boot
bands.
Clearance
(A) : 2.0 mm (0.079 in.) or
less
|
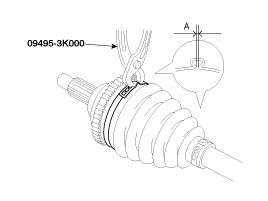
|
5. |
To reassemble the dynamic damper, keeping
the shaft in the straight, tighten the dynamic damper with dynamic
damper band, as the illustration.
Distance
(L) : 228.4 ~ 228.6mm (8.99 ~
9.00in)
|
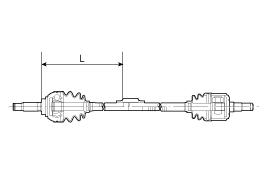
|
6. |
Install the PTJ boot bands and PTJ
boot. |
7. |
Install the trunion assembly (A) and the
circlip (E) to the spline (C) on the driveshaft.
At this time align the marks (D) each
other.
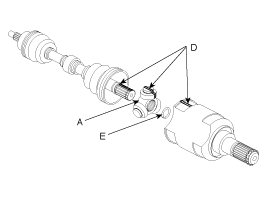
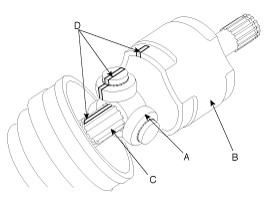
|
8. |
Install the clip to the PTJ case
(B). |
9. |
Add the specified grease to the PTJ as mush
as wiped away at inspection. |
10. |
Install the PTJ
boots. |
11. |
To control the air in the PTJ boot, keep the
specified distance between the boot bands when they are
tightened.
Distance
(A)
|
LH side
|
RH
side
|
Diesel 3.0, Gasoline
3.8 (mm(in))
|
530.5 +27.9 -22.5 (20.89
+1.10 -0.89)
|
543.5 +27.9 -22.5 (21.40
+1.10 -0.89)
|
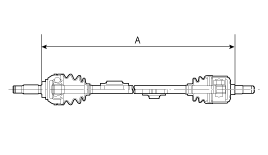
|
12. |
Install the bands to both PTJ
boots.
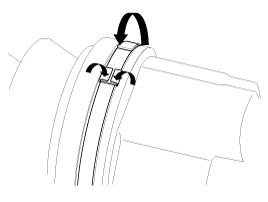
| |