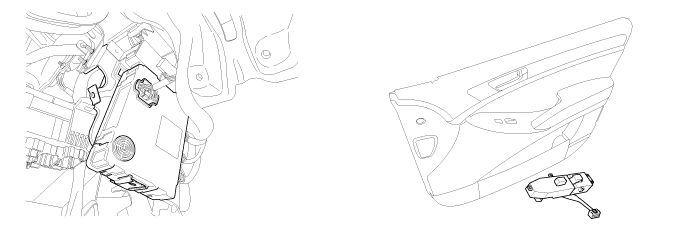
The 6 components related
with Body Control Module(hereinafter referred to BCM) connect with each
other via CAN(Controller Area Network) communication system. These are
BCM. Assist Door Module (ADM), Drive Door Module (DDM), Power Seat Unit
(PS), tilt/telescope control unit and Personal Identification Card
(PIC).
Wiper Motor Module (WMM)
and Mulit-Function Switch (M/F) connect with BCM via LIN (Local
Interconnect Network). Therefore it is possible to diagnose an overall
system with scantool.
*¹ CAN (Cotroller Area
Network) : CAN is a serial bus system especially suited for networking
"intelligent" devices as well as sensors and actuators within a system or
sub-system.
*² LIN (Local
Interconnect Network) : LIN is a new low cost serial communication system
intended to be used for distributed electronic systems in vehicles, which
complements the existing portfolio of automotive multiplex
networks.
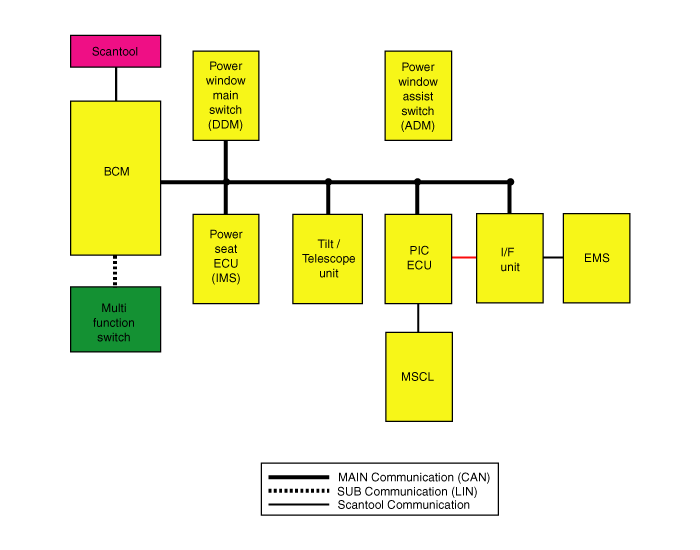
This code means that
there is a problem in CAN BUS between BCM and ADM. This code is set if ADM
message is not transmitted for more than 10s. Possible cause is
disconnected connector and open circuited in CAN HIGH, LOW
line.
Item
|
Detecting
Condition
|
Possible cause
|
DTC
Strategy
|
•
|
Check CAN communition
state. | |
•
|
Open circuited in CAN HIGH, LOW
line. |
|
Enable
Conditions
|
•
|
Unable to transmit data via CAN
line. | |
Threshold
Value
|
•
|
Both CAN High and Low line are open
circuited. | |
Diagnostic
Time
|
|
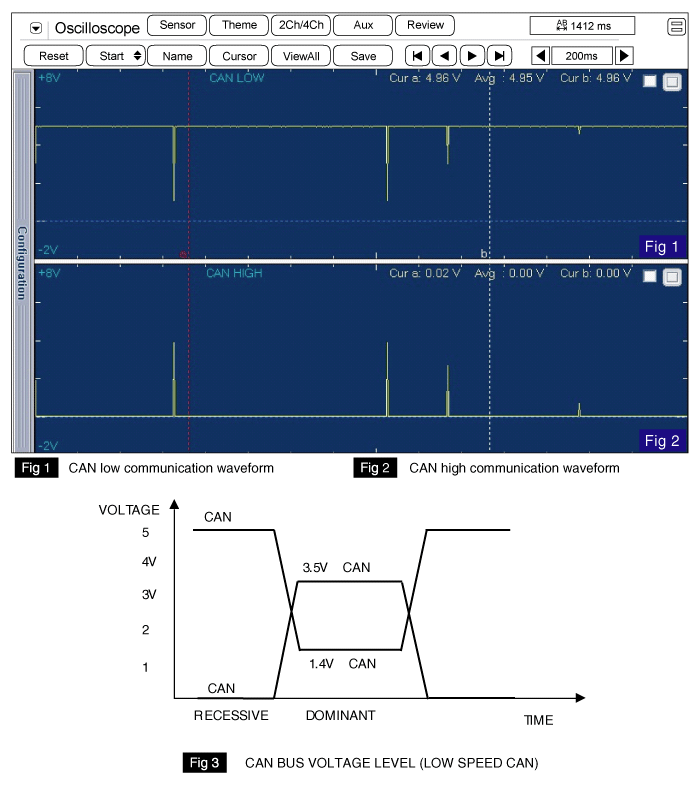
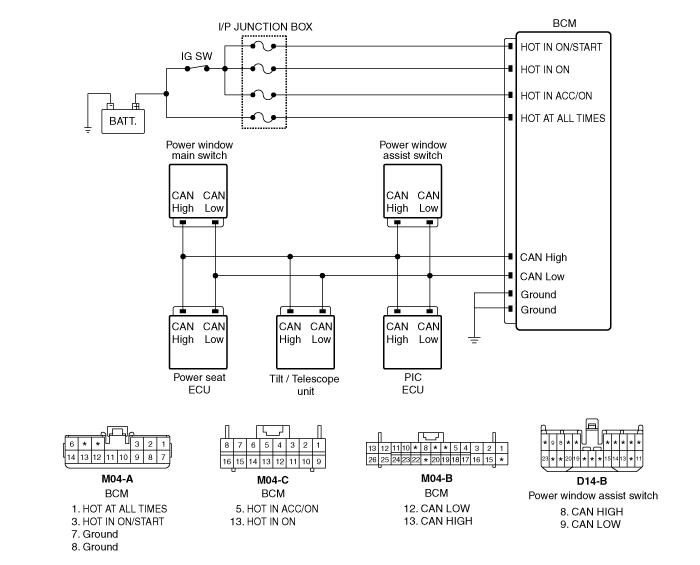
1. |
Ignition "OFF", connect
scantool. |
2. |
Ignition "ON" & Engine "OFF", select
"Diagnostic Trouble Codes(DTC)"
mode. |
3. |
Monitor diagnostic trouble code and present of
trouble code. |
4. |
Using a scan tool, clear the DTC.
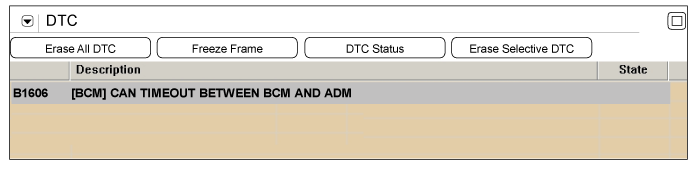
|
5. |
Are any DTC present?

|
▶ Go to
"W/Harness Inspection" procedure.
|

|
▶
Displaying nothing(no DTC) shows that Fault is intermittent
caused by poor contact in the part's and/or ADM connector or
was repaired and BCM memory was not cleared. Thoroughly check connectors for looseness, poor
connection, bending, corrosion, contamination, deterioration,
or damage. ▶ Repair or replace as
necessary and then go to "Verification of Vehicle Repair"
procedure.
|
|
Terminal And Connector
Inspection |
1. |
Many malfunctions in the electrical system are
caused by poor harness(es) and terminals. Faults can also be caused
by interference from other electrical systems and mechanical or
chemical damage. |
2. |
Check the following conditions:
(1) |
Check for damaged harness and terminals:
contact resistance, oxidation, bent or broken
terminals. |
(2) |
Check for poor connection between ECM
and component: backed out terminal, improper mating, broken
locks and poor terminal to wire
connection. |
Using a suitable male pin to ensure that
contact in sockets is good. The pin should remain in position
when pulled
gently. | |
3. |
Has a problem been found?

|
▶ Repair as
necessary and then go to "Verification of Vehicle Repair"
procedure.
|

|
▶ Go to
"ADM Signal Circuit Inspection"
procedure.
|
|
ADM Signal Circuit
Inspection |
1. |
Check CAN high communication
circuit
(1) |
Ignition "ON" and Engine
"OFF" |
(2) |
Connect scantool and select VEHICLE
SCOPEMETER function. |
(3) |
Measure waveform between "CAN high" of
ADM connector and chassis ground.
Specification : If
CAN high communication waveform is displayed, it is
OK.
| |
(4) |
Is CAN high communication waveform
displayed within specification?

|
▶ Go
to "Check CAN low communication circuit" as
below.
|

|
▶
Repair the short to ground or battery in the CAN
communication circuit and go to "Verification of Vehicle
Repair".
|
| |
2. |
Check CAN low communication
circuit
(1) |
Ignition "ON" and Engine
"OFF" |
(2) |
Connect scantool and select VEHICLE
SCOPEMETER function. |
(3) |
Measure waveform between "CAN Low" of
ADM connector and chassis ground.
Specification : If
CAN low communication waveform is displayed, it is
OK.
| |
(4) |
Is CAN communication waveform displayed
within specification?

|
▶ Go
to "Component Inspection" procedure.
|

|
▶
Repair the short to ground or battery or CAN high
communication circuit and go to "Verification of Vehicle
Repair".
|
| |
1. |
Check CAN communication ECU's internal
error
(1) |
Ignition "ON" and engine
"OFF". |
(2) |
Connect scantool and select DIAGNOSIS
TROUBLE CODE. |
(3) |
Substitute a known-good DDM, and check
for proper operation. |
(4) |
Is CAN ERROR DTC cleared?

|
▶
Substitute with a known-good one of them and check
proper condition. If the
problem is corrected, replace one of them and then go to
"Verification of Vehicle Repair"
procedure.
|

|
▶
Thoroughly check connectors for looseness, poor
connection, bending, corrosion, contamination,
deterioration or damage. Repair or replace as necessary and then go to
"Verification of Vehicle Repair"
procedure.
|
| |
Verification Of Vehicle
Repair |
After a repair, it is
essential to verifying that the fault has been corrected.
1. |
Connect scan tool and select "Diagnostic
Trouble Codes(DTCs)" mode. |
2. |
Using scantool, Clear
DTC. |
3. |
Operate the vehicle within DTC Enable
conditions in General information. |
4. |
Are any DTCs present ?

|
▶ Go to the
applicable troubleshooting procedure.
|

|
▶ System is
performing to specification at this
time.
|
|