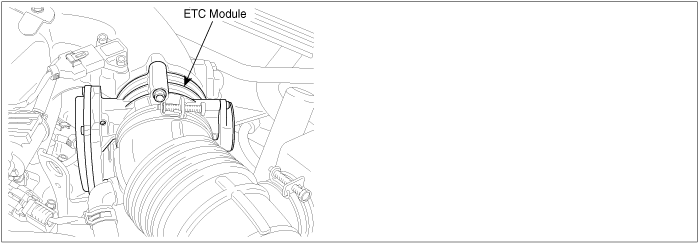
The Electronic Throttle
Control(ETC) system is made of the components throttle body, Throttle
Position Sensor(TPS)1&2 and Accelerator Position Sensor(APS) 1&2.
TPS1&2 are sharing the same source voltage and ground.The throttle
valve opening is control by throttle motor which is controlled by Engine
Control Module(PCM).The opposite position indicator shows inverted signal
characteristics.TPS1 output voltage increases smoothly in proportion with
the throttle valve opening angle after starting. TPS2 output voltage
decreases in inverse proportion with the throttle valve opening angle
after starting. TPS provides feedback to the PCM to control the throttle
motor in order to control the throttle valve opening angle properly in
response to the driving condition.
Checking output signals
from TPS2 every 8.5 sec. under detecting condition, if an output signal is
above 4.75V for more than 0.1 sec., PCM sets P0223. MIL(Malfunction
Indication Lamp) turns on when the malfunction lasts till consecutive 2
driving cycle.
Item
|
Detecting
Condition
|
Possible Cause
|
DTC
Strategy
|
|
•
|
Short to battery in signal
harness |
|
Enable
condition
|
|
threshold
value
|
•
|
The signal voltage of TPS
>4.75V | |
diagnosis
time
|
•
|
Continuous
(more than 0.1 sec. failure for every
8.5 sec.test) | |
MIL ON
condition
|
|
Throttle opening ( °
)
|
Output voltage(V)
[Vref=5.0]
|
TPS1
|
TPS2
|
0°
|
0.0V
|
5.0V
|
10°
|
0.5V
|
4.5V
|
20°
|
0.9V
|
4.1V
|
30°
|
1.4V
|
3.6V
|
40°
|
1.8V
|
3.2V
|
50°
|
2.3V
|
2.7V
|
60°
|
2.7V
|
2.3V
|
70°
|
3.2V
|
1.8V
|
80°
|
3.6V
|
1.4V
|
90°
|
4.1V
|
0.9V
|
100°
|
4.5V
|
0.5V
|
110°
|
5.0V
|
0.0V
|
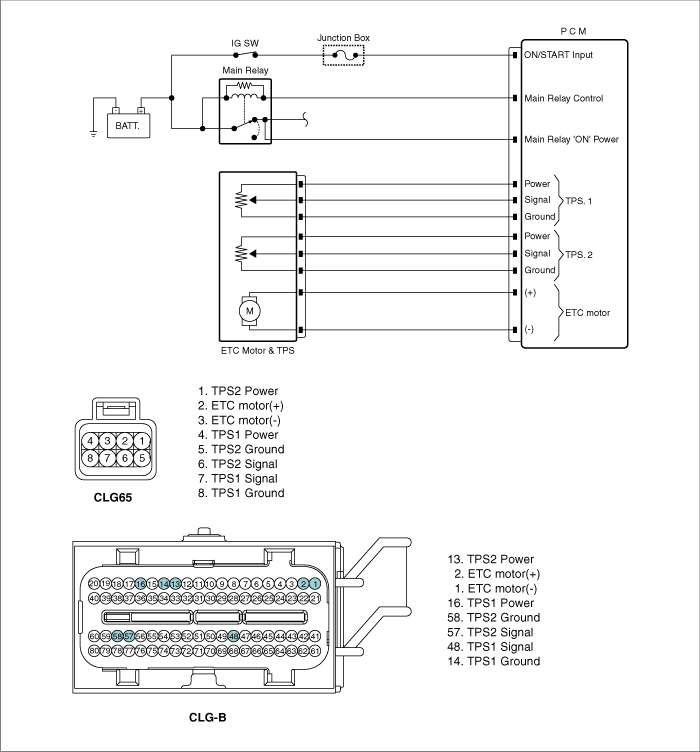
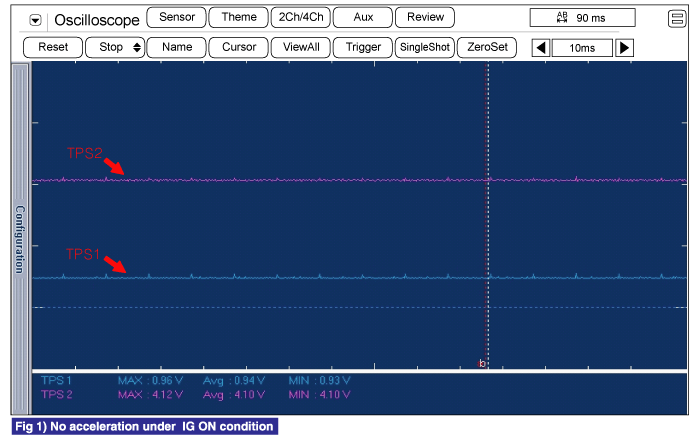
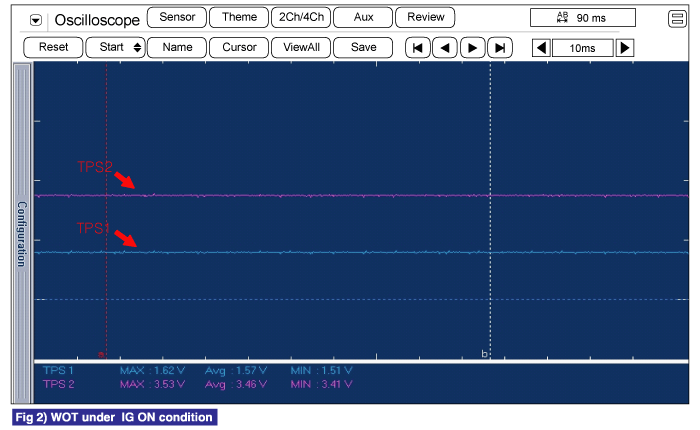
1. |
Check DTC Status
(1) |
Connect scantool to Data Link
Connector(DLC). |
(3) |
Select "DTC" button, and then Press "DTC
Status" to check DTC's information from the DTCs
menu. |
(4) |
Read "DTC Status"
parameter.
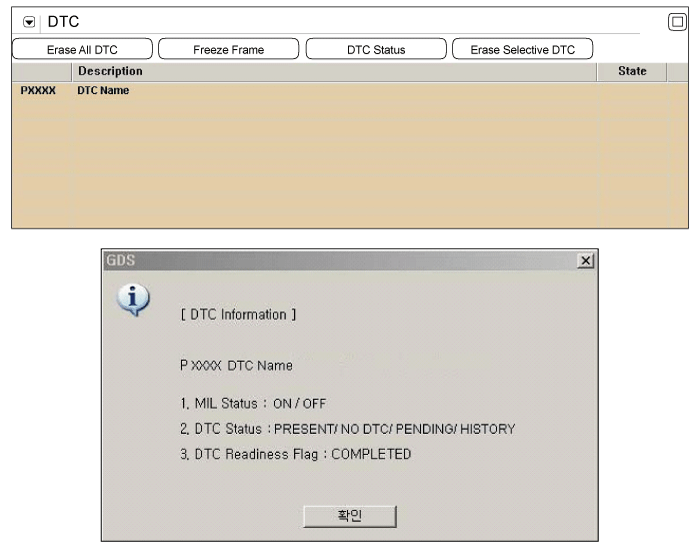
|
(5) |
Is parameter displayed "Present
fault"?

|
▶ Go
to "Terminal and connector inspection"
procedure.
|

|
▶
Fault is intermittent caused by poor contact in the
sensor's and/or PCM's connector or was repaired and PCM
memory was not cleared. Thoroughly check connectors for
looseness, poor connection, ending, corrosion,
contamination, deterioration, or damage. Repair or
replace as necessary and go to "Verification of Vehicle
Repair"
procedure.
|
| |
Terminal And Connector
Inspection |
1. |
Many malfunctions in the electrical system are
caused by poor harness and terminal condition. Faults can also be
caused by interference from other electrical systems, and mechanical
or chemical damage. |
2. |
Thoroughly check connectors for looseness,
poor connection, bending, corrosion, contamination, deterioration,
or damage. |
3. |
Has a problem been found?

|
▶ Repair as
necessary and go to "Verification of Vehicle Repair"
procedure
|

|
▶ Go to
"Signal Circuit Inspection"
procedure.
|
|
Signal Circuit
Inspection |
■ Check Voltgae
1. |
IG "OFF" and disconnect ETC Motor & TPS
connector. |
3. |
Measure voltage between TPS2 signal terminal
of ETC Motor & TPS harness connector and chassis
ground.
Specification
: Approx. 0V
| |
4. |
Is the measured voltage within
specification?

|
▶ Go to
"Ground Circuit Inspection" procedure.
|

|
▶ Go to
"Check short to battery in harness" as
follows.
|
|
■ Check short to battery in harness
1. |
IG "OFF" and disconnect ETC Motor & TPS
connector and PCM connector. |
2. |
Measure resistance between TPS2 signal and
TPS1 power terminals of ETC Motor & TPS harness
connector.(Measurement "A") |
3. |
Measure resistance between TPS2 signal and
TPS2 power terminals of ETC Motor & TPS harness
connector.(Measurement "A") |
4. |
Measure resistance between TPS2 signal and ETC
motor(+) terminals of ETC Motor & TPS harness
connector.(Measurement "B") |
5. |
Measure resistance between TPS2 signal and ETC
motor(-) terminals of ETC Motor & TPS harness
connector.(Measurement "B")
|
6. |
Is the measured resistance within
specification?

|
▶ Go to "
Ground Circuit Inspection" procedure.
|

|
▶ Repair
short to battery in harness, and go to "Verification of
Vehicle Repair"
procedure.
|
|
Ground Circuit
Inspection |
■ Check open in harness
1. |
IG "OFF" and disconnect ETC Motor & TPS
connector. |
3. |
Measure voltage between TPS2 power terminal of
ETC Motor & TPS harness connector and chassis
ground.(Measurement "A") |
4. |
Measure voltage between TPS2 power and TPS2
ground terminals of ETC Motor & TPS harness
connector.(Measurement "B")
Specification
: Voltage difference between
measurement "A" and "B" is below 200mV.
| |
5. |
Is the measured voltage within
specification?

|
▶ Go to
"Component Inspection" procedure.
|

|
▶ Repair
open or contact resistance inharness, and go to "Verification
of Vehicle Repair:
procedure.
|
|
■ Check TPS resistance
1. |
IG "OFF" and disconnect ETC Motor & TPS
connector. |
2. |
Measure resistance between TPS2 power and TPS2
ground terminals of ETC Motor & TPS connector.(component
side)
Specification
: 2.7 ~ 4.1kΩ
| |
3. |
Is the measured resistance within
specification?

|
▶
Substitute with a known - good PCM and check for proper
operation. If the problem is corrected, replace PCM and go to
"Verification of Vehicle Repair" procedure.
|

|
▶
Substitute with a known - good TPS and check for proper
operation. If the problem is corrected, replace TPS and go to
"Verification of Vehicle Repair"
procedure.
|
There is a memory reset function on
scantool that can erase optional parts automatically detected
and memorized by PCM. After testing PCM on the vehicle, use
this function before reusing the
PCM |
Procedure of ETS
Initialization
1. |
Erase the trouble codes on
PCM |
2. |
Turn the ignition key off and keep
this condition until the main relay is turned off.(10
sec.) |
3. |
Turn ignition key on more than
1second to record the throttle motor position on the
EEPROM | | |
Verification Of Vehicle
Repair |
After a repair, it is
essential to verify that the fault has been corrected.
1. |
Connect scantool and select "DTC"
button. |
2. |
Press "DTC Status" button and confirm that
"DTC Readiness Flag" indicates "Completed". If not, drive the
vehicle within conditions noted in the freeze frame data or enable
conditions |
3. |
Read "DTC Status"
parameter |
4. |
Is parameter displayed "History(Not Present)
fault"?

|
▶ System
performing to specification at this time. Clear the
DTC
|

|
▶ Go to the
applicable troubleshooting
procedure.
|
|