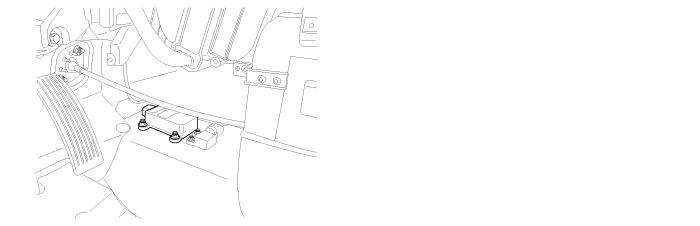
When the vehicle is
turning with respect to a vertical axis the yaw rate sensor detects the
yaw rate electroniclly by the vibration change of plate fork inside the
yaw rate sensor.
If yaw velocity reaches
the specific velocity after it detects the vehicle' yawing, the ESC
control is reactivated.
The later G sensor
senses vehicle's lateral G. A small element inside the sensor is attached
to a deflectable leverarm by later G.
Direction and magnitude
of lateral G loaded to vehicle can be known with electrostatic capacity
changing according to lateral G.
It interchanges signals
with HECU through extra CAN line which only used for communication between
HECU and sensor.
A lateral acceleration
reference signal is calculated from the wheel speeds, the steering angle
and the yaw rate signals to observe the lateral acceleration sensor
signal.
The difference between
the reference signal and the sensor signal is evaluated for failure
detection. A yaw rate reference signal is calculated from the wheel
speeds, the steering angle and the lateral acceleration signals to observe
the yaw rate sensor signal.
The difference between
the reference signal and the sensor signal, and the gradient of the
measured sensor signal is evaluated for the failure
detection.
If the difference
between estimated value and measured value of the sensor is larger than
predefined value for predefined time, the failure is
recognized.
Item
|
Detecting
Condition
|
Possible cause
|
DTC Strategy
|
|
•
|
Faulty Yaw Rate & Lateral G
sensor | |
Case1
|
Enable Conditions
|
•
|
When the difference between estimated
value and measured value of the yaw rate sensor is lager than
Predefined value for specific time , ECU detects
failure. | |
Case2
|
Enable Conditions
|
•
|
When the difference between estimated
value and measured value of the lateral G sensor is lager than
Predefined value for specific time , ECU detects
failure. | |
Case3
|
Enable Conditions
|
•
|
Yaw signal is smaller than predefined
value when CBIT is
transmitted |
•
|
Lateral G signal is smaller than defined
value when CBIT is transmitted.
※ CBIT : Commanded Built In
Test | |
Case4
|
Enable Conditions
|
•
|
In case that Yaw& Lateral G Sensor
Fail Flag is detected for defined
time | |
Fail Safe
|
•
|
Inhibit the ESC control and allow the
ABS/EBD control. |
•
|
The ESC warning lamp is
activated. | |
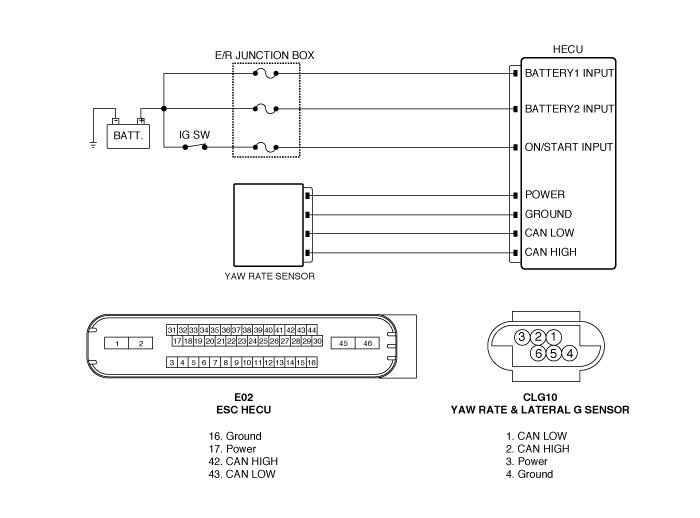
1. |
Connect scantool to Data Link
Connector(DLC). |
2. |
Ignition "ON" & Engine
"OFF". |
3. |
Monitor the "Lateral G Sensor, Yaw Rate
Sensor" parameter on the Scantool.
Specification
: Lateral G Sensor : approx. ± 0.0 G,
YAW Rate Sensor :approx. ± 0.0 deg/s
|
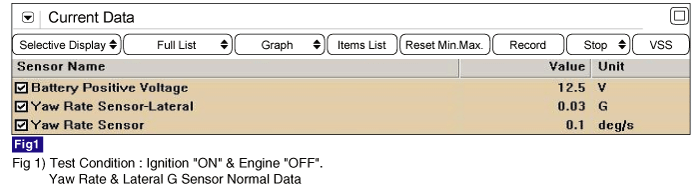
|
4. |
Is parameter displayed within
specifications?

|
▶ Fault is
intermittent caused by poor connection in Yaw Rate &
Lateral G sensor harness and/or HECU's connector or was
repaired and HECU memory was not cleared. Thoroughly check connectors for looseness, poor
connection, bending, corrosion, contamination, deterioration,
or damage. Repair or replace as
necessary and then go to "Verification Of Vehicle Repair"
procedure.
|

|
▶ Go to
"Terminal and Connector Inspection"
procedure.
|
|
Terminal and Connector
Inspection |
1. |
Many malfunctions in the electrical system are
caused by poor harness(es) and terminal condition. Faults can also
be caused by interference from other electrical systems, and
mechanical or chemical damage. |
2. |
Thoroughly check connectors for looseness,
poor connection, bending, corrosion, contamination, deterioration,
or damage. |
3. |
Has a problem been found?

|
▶ Repair as
necessary and then go to "Verification Of Vehicle Repair"
procedure.
|

|
▶ Go to
"Component Inspection"
procedure.
|
|
Component Circuit
Inspection |
2. |
Ignition "ON" & Engine
"OFF". |
3. |
Operate the vehicle within DTC Detecting
Condition in General Information. (Start and drive vehicle in gear
and maintain vehicle speed at or above 40kmh.
(24mph)) |
4. |
Using a scantool, Clear
DTC. |
5. |
Select "Diagnostic Trouble Codes(DTCs)" mode
again. |
6. |
Are any DTCs present ?

|
1. |
Substitute with a known-good Yaw
Rate & Lateral G sensor and check for proper
operation.
If problem is corrected, replace
Yaw Rate & Lateral G sensor and then go to
"Verification Of Vehicle Repair"
procedure. |
2. |
Substitute with a known-good HECU
and check for proper operation.
If problem is corrected, replace
HECU and then go to "Verification Of Vehicle Repair"
procedure. | |

|
▶ Fault is
intermittent caused by faulty Yaw Rate & Lateral G sensor
or poor connection in Yaw Rate & Lateral G sensor harness
and/or HECU's connector. Go to "Verification Of Vehicle
Repair"
procedure.
|
|
Verification of Vehicle
Repair |
After a repair, it is
essential to verify that the fault has been corrected.
1. |
Connect scantool and select "Diagnostic
Trouble Codes(DTCs)" mode. |
2. |
Using a scantool, Clear
DTC. |
3. |
Operate the vehicle within DTC Detecting
Condition in General Information. (Start and drive vehicle in gear
and maintain vehicle speed at or above 40kmh.
(24mph)) |
4. |
Using a scantool, Check DTC
present. |
5. |
Are any DTCs present ?

|
▶ Go to the
applicable troubleshooting procedure.
|

|
▶ System
performing to specification at this
time.
|
|