1. |
Disconnect the (-) terminal from the
battery. |
3. |
Remove the front muffler (A). (refer to
Intake And Exhaust System in EM group)
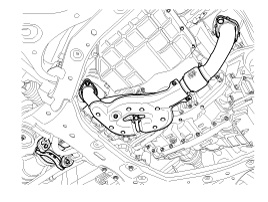
|
4. |
Disconnect the propeller shaft (A) by
removing the three bolts.
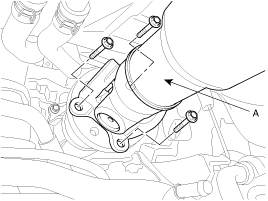
|
5. |
Disconnect the right driveshaft from the
transfer case. (refer to Drive shaft in DS
group) |
6. |
Drain the fluid by removing the oil drain
plug (A).
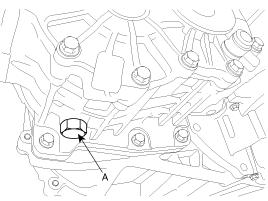
|
7. |
After completing draining the fluid, install
the oil drain plug.
Torque : 40-60 Nm (4.0-6.0 kgf.m,
28.9-43.4 lb-ft)
| |
8. |
Remove the four mounting bolts (A) of
transfer case bracket.
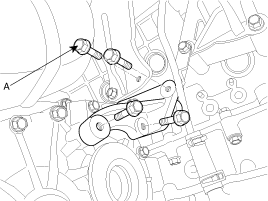
|
9. |
Remove the transfer case assembly by
removing the six mounting bolts (A).
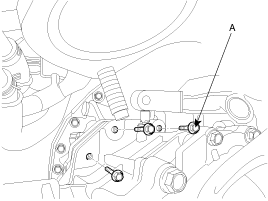
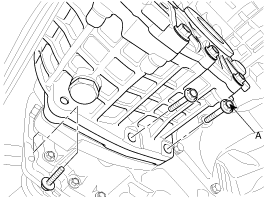
|
Must use a new O-ring
(47354-39300). |
1. |
Temporarily install the transfer case
assembly to the transaxle and then tighten the six mounting bolts
(A).
Torque : 62-67 Nm (6.2-6.7 kgf.m,
44.8-48.5 lb-ft)
|
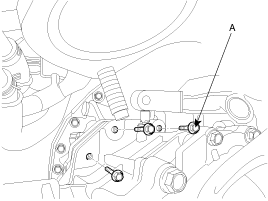
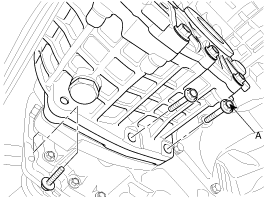
|
2. |
Install the four mounting bolts (A) of the
transfer case bracket.
Torque : 47-51 Nm (4.7-5.1 kgf.m,
34.0-36.9 lb-ft)
|
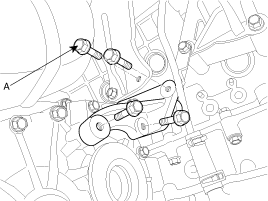
|
3. |
Remove the filler plug (A).
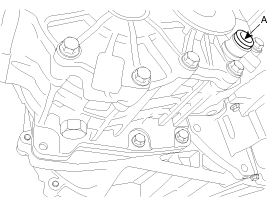
|
4. |
After refilling the fluid amount of the
specified, tighten the filler plug.
Specification : API GL-5, SAE
75W/90
Quantity : Approx
0.8L
| |
5. |
Install the right driveshaft to the transfer
case. (refer to Drive shaft in DS
group) |
6. |
Install the propeller shaft (A) to the
transfer case.
Torque : 50-70 Nm (5.0-7.0 kgf.m,
36.2-50.6 lb-ft)
|
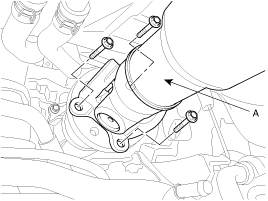
|
7. |
Install the front muffler (A). (refer to
Intake And Exhaust System in EM group)
Torque : 40-60 Nm (4.0-6.0 kgf.m,
28.9-43.4 lb-ft)
|
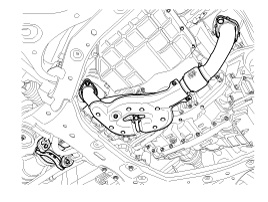
|
8. |
Connect the (-) terminal to the
battery. |
1. |
Drain the transfer oil through drain plug
hole. |
2. |
Remove the pinion assembly mounting bolts
(7EA) and then remove the pinion assembly(A).
This assembly can be removed with a
propeller shaft assembly in 'REMOVAL'
step. |
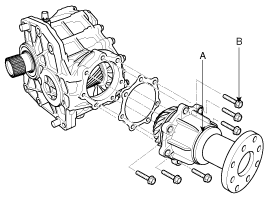
|
3. |
Remove the dust cover(A).
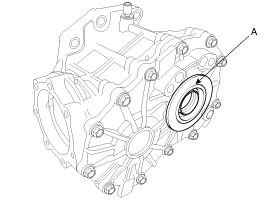
|
4. |
Remove the transfer cover(A).
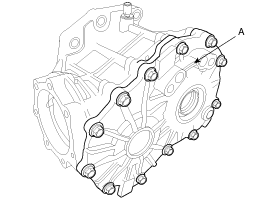
|
5. |
Remove the transfer drive gear assembly(A)
and the hypoid gear shaft assembly(B) from the trasfer
housing.
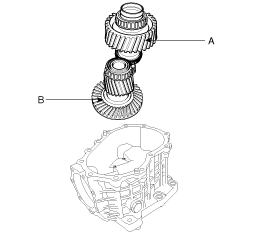
|
6. |
Remove the oil seal(A)(transfer drive gear
left hand side).
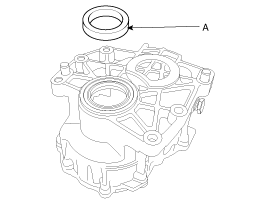
|
7. |
Using a sliding hammer, remove the taper
roller bearing outer races(C) from the transfer cover(A) and
housing(B).
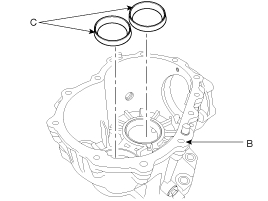
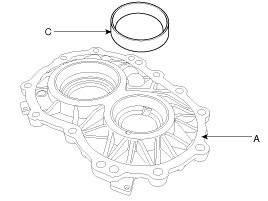
|
8. |
Remove the oil seal(A) from the transfer
cover.
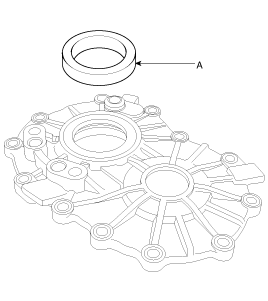
|
1. |
Clean all parts except the taper
roller bearings. Be careful about the direction of
seals. |
2. |
Oil bearings with hypoid gear oil API
GL5. |
3. |
Smear involute splines all covering
with high pressure grease "Klueber microlube
GNY202". |
4. |
Measuring temperature:
20°±5°C. |
5. |
O-ring has to be dipped into hypoid
gear oil API GL5. Allow excess oil to
drain. |
6. |
Contact surface of the transfer
housing to be coated with "SEALANT 732" or equivalent (silicon
type sealing agent) prior to mounting. Coating thickness:
0.1mm MIN. Prior to coating, mating surfaces must be clean and
free from oil and grease. |
7. |
Transfer oil specification : Hypoid
gear oil "API GL5, SAE 75W/90 SHELL SPIRAX X EQUIVALENT".
Filled up to lower filler plug thread level( Approx.
0.8L) |
8. |
The hypoid gear set must be managed as
a pair. Whenever installing or replacing a hypoid gear shaft
assembly(47308-24000/24010) or a pinion
shaft(47311-39300/39310). Make sure to install or replace as a
pair. |
9. |
In reassembling, refer to the two
figures
below. | |
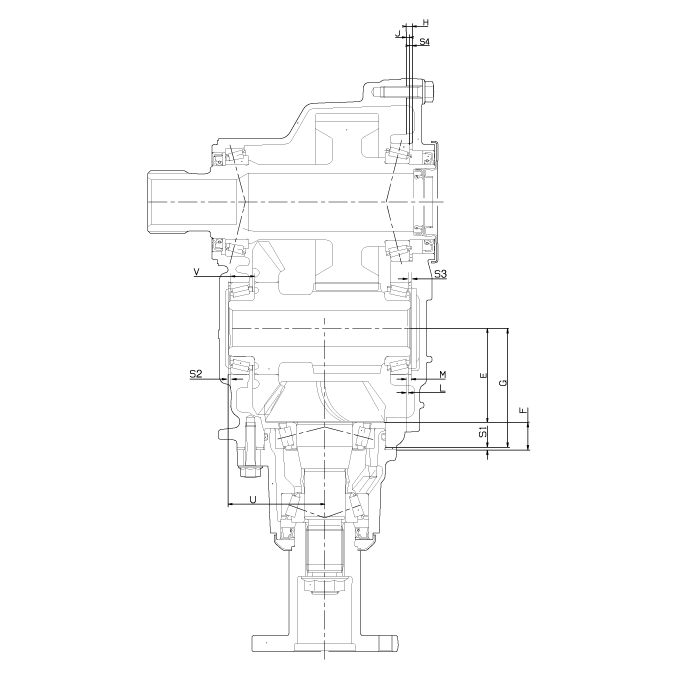
1. |
Install the transfer drive gear with the
taper roller bearings(47366-39000 and 47465-39000) into transfer
housing. |
2. |
Applying the preload(100 to 200N) to
bearings, measure the dimension J. |
3. |
Measure the dimension H on transfer
cover(47314-24000). |
4. |
Select the spacer thickness from the chart
below. Thickness S4= H-J+K. (K: Bearing preload = 0.07 to 0.11mm.
)
Corresponding preload torque(measured
without seals) : 120 to 180Ncm.
Part number
|
Spacer thickness(mm)
|
47383-39152
|
1.520-1.539
|
47383-39154
|
1.540-1.559
|
47383-39156
|
1.560-1.579
|
47383-39158
|
1.580-1.599
|
47383-39160
|
1.600-1.619
|
47383-39162
|
1.620-1.639
|
47383-39164
|
1.640-1.659
|
47383-39166
|
1.660-1.679
|
47383-39168
|
1.680-1.699
|
47383-39170
|
1.700-1.719
|
47383-39172
|
1.720-1.739
|
47383-39174
|
1.740-1.759
|
47383-39176
|
1.760-1.779
|
47383-39178
|
1.780-1.779
|
47383-39180
|
1.800-1.819
|
47383-39182
|
1.820-1.839
|
47383-39185
|
1.85-1.88
|
47383-39189
|
1.89-1.92
|
47383-39193
|
1.93-1.96
|
47383-39197
|
1.97-2.00
|
47383-39201
|
2.01-2.04
|
47383-39205
|
2.05-2.08
|
47383-39209
|
2.09-2.12
|
47383-39213
|
2.13-2.16
|
47383-39217
|
2.17-2.20
|
47383-39221
|
2.21-2.24
|
47383-39225
|
2.25-2.28
|
47383-39229
|
2.29-2.32
|
47383-39233
|
2.33-2.36
|
|
5. |
Reassemble the selected spacer
above. |
6. |
Measure the dimension U and V.
U…. Finished
dimension of transfer housing.
V…. Distance from
back of the hypoid gear to bearing measured under 100 to 200N
preload. |
7. |
Select the spacer thickness from the chart
below. Thickness S2=U-(V + mounting distance 52.0 mm).
Part number
|
Spacer thickness(mm)
|
47384-39130
|
1.300-1.319
|
47384-39134
|
1.340-1.359
|
47384-39138
|
1.380-1.399
|
47384-39142
|
1.420-1.439
|
47384-39146
|
1.460-1.479
|
47384-39148
|
1.480-1.499
|
47384-39150
|
1.500-1.519
|
47384-39152
|
1.520-1.539
|
47384-39154
|
1.540-1.559
|
47384-39156
|
1.560-1.579
|
47384-39158
|
1.580-1.599
|
47384-39160
|
1.600-1.619
|
47384-39162
|
1.620-1.639
|
47384-39164
|
1.640-1.659
|
47384-39166
|
1.660-1.679
|
47384-39168
|
1.680-1.699
|
47384-39170
|
1.700-1.719
|
47384-39174
|
1.740-1.759
|
47384-39178
|
1.780-1.799
|
47384-39182
|
1.820-1.839
|
47384-39186
|
1.860-1.879
|
47384-39190
|
1.900-1.919
|
47384-39194
|
1.940-1.959
|
47384-39198
|
1.980-1.999
|
47384-39200
|
2.000-2.019
|
47384-39202
|
2.020-2.039
|
47384-39204
|
2.040-2.059
|
47384-39206
|
2.060-2.079
|
47384-39208
|
2.080-2.099
|
47384-39210
|
2.100-2.119
|
|
8. |
Install the spacer selected above, the taper
roller bearings and the hypoid gear shaft assembly
(47308-24000/24010). And preload the assembly without the
spacer(Hypoid gear shaft assembly-Transfer cover side) with 100 to
200N. |
9. |
Measure the dimension L after 10
rotations. |
10. |
Measure the dimension M on transfer cover
(47314-24000). |
11. |
Select the spacer thickness from the chart
below. Thickness S3=M-L+(0.09 to 0.12mm) preload.
Part number
|
Spacer thickness(mm)
|
47388-24130
|
1.300-1.319
|
47388-24132
|
1.320-1.339
|
47388-24134
|
1.340-1.359
|
47388-24136
|
1.360-1.379
|
47388-24138
|
1.380-1.399
|
47388-24140
|
1.400-1.419
|
47388-24142
|
1.420-1.439
|
47388-24144
|
1.440-1.459
|
47388-24146
|
1.460-1.479
|
47388-24148
|
1.480-1.499
|
47388-24150
|
1.500-1.519
|
47388-24152
|
1.520-1.539
|
47388-24154
|
1.540-1.559
|
47388-24156
|
1.560-1.579
|
47388-24158
|
1.580-1.599
|
47388-24160
|
1.600-1.619
|
47388-24162
|
1.620-1.639
|
47388-24164
|
1.640-1.659
|
47388-24166
|
1.660-1.679
|
47388-24168
|
1.680-1.699
|
47388-24170
|
1.700-1.719
|
47388-24172
|
1.720-1.739
|
47388-24174
|
1.740-1.759
|
47388-24176
|
1.760-1.779
|
47388-24178
|
1.780-2.799
|
47388-24180
|
1.800-2.819
|
47388-24182
|
1.820-2.839
|
47388-24184
|
1.840-2.859
|
47388-24186
|
1.860-2.879
|
47388-24250
|
2.50-2.53
|
|
12. |
Install the spacer selected
above. |
13. |
Install the taper roller bearing outer races
to the transfer housing and cover. |
14. |
Install a new oil seal(A) in the transfer
housing.
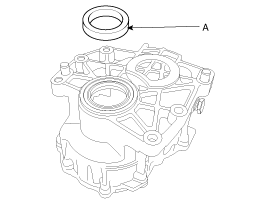
|
15. |
Install the transfer drive gear shaft
assembly(A) and the hypoid gear assembly(B) in the transfer
housing.
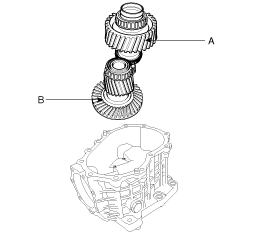
|
16. |
Measure the dimension F.
F…. Assembled
dimension of pinion assembly.
G…. Finished
dimension of transfer housing.(=88.0mm)
E…. Mounting
distance(=69.500 ± deviation). |
17. |
Select the spacer thickness from the chart
below. Thickness S1=E+F-G
If it is not possible to reach the
exact mounting distance, select the next thinner spacer
S1. |
Part number
|
Spacer thickness(mm)
|
47386-39125
|
1.25-1.28
|
47386-39129
|
1.29-1.32
|
47386-39133
|
1.33-1.36
|
47386-39137
|
1.37-1.40
|
47386-39141
|
1.41-1.44
|
47386-39145
|
1.45-1.48
|
47386-39149
|
1.49-1.52
|
47386-39153
|
1.53-1.56
|
47386-39157
|
1.57-1.60
|
47386-39161
|
1.61-1.64
|
47386-39165
|
1.65-1.68
|
47386-39169
|
1.69-1.72
|
47386-39172
|
1.720-1.739
|
47386-39174
|
1.740-1.759
|
47386-39176
|
1.760-1.779
|
47386-39178
|
1.780-1.799
|
47386-39180
|
1.800-1.819
|
47386-39182
|
1.820-1.839
|
47386-39184
|
1.840-1.859
|
47386-39186
|
1.860-1.879
|
47386-39188
|
1.880-1.899
|
47386-39190
|
1.900-1.919
|
47386-39192
|
1.920-1.939
|
47386-39194
|
1.940-1.959
|
47386-39196
|
1.960-1.979
|
47386-39198
|
1.980-1.999
|
47386-39200
|
2.000-2.019
|
47386-39202
|
2.020-2.039
|
47386-39204
|
2.040-2.059
|
47386-39233
|
2.33-2.36
|
|
18. |
Install the pinion assembly with the
selected spacer above and measure the circumference backlash on
pinion.
(Measuring diameter, backlash and
permissible deviations for measurement on pinion, see table
below).
If the result is out of permissible range,
change the spacer thickness S2, then start again with the step
8~12).
Tips for spacer adjustment for hypoid gear backlash and
contact pattern
ITEM
|
SYMPTOM
|
REMEDY
|
Backlash
|
When more than the standard value (0.16 ~
0.21mm)
|
Adjust backlash by installing the spacer S1 using
a thinner one and gradually installing a thicker
one.
|
When less than the standard value (0.16
~0.21mm)
|
Adjust backlash by installing the spacer S1 using
a thicker one and gradually installing a thinner
one.
|
ITEM
|
SYMPTOM
|
REMEDY
|
Hypoid gear tooth contact
pattern
|
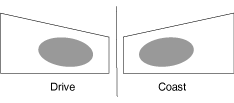
|
- |
Both drive and coast
surfaces are in center in lateral direction and
slightly incline to TOE side in vertical
direction | |
• |
If the pattern deviates from the
standard, adjust it by following
procedure | |
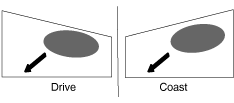
|
• |
The drive surface inclines to
TOE and TOP and the coast surface inclines to HEEL and
TOP | The tooth contact pattern can be moved to the
arrow direction by installing the spacer S2 using a thinner
one and gradually installing a thicker
one.
|
|
19. |
Remove the pinion assembly. With the spacer
S3 and transfer cover mounted, combined preload torque for the
hypoid gear shaft assembly and transfer gear (measured on transfer
gear) should be 2.7 to 3.8Nm. The spacer S3 has to be changed, if
the preload torque is not within the permissible
range. |
20. |
Tighten the pinion assembly mounting bolts
(B-7EA) to install the pinion assembly(A).
TORQUE:
37~40 Nm(3.7~4.0 kgf.m, 14.5~21.7
lb-ft)
|
1. |
Before installing the pinion
assembly, check the pinion O-ring and apply the oil to
the O-ring. |
2. |
To make the installation of the
pinion to the transfer easier, tap the pinion using a
plastic hammer after aligning the bolt
holes. | |
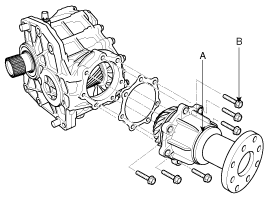
| |